Drilling fluid
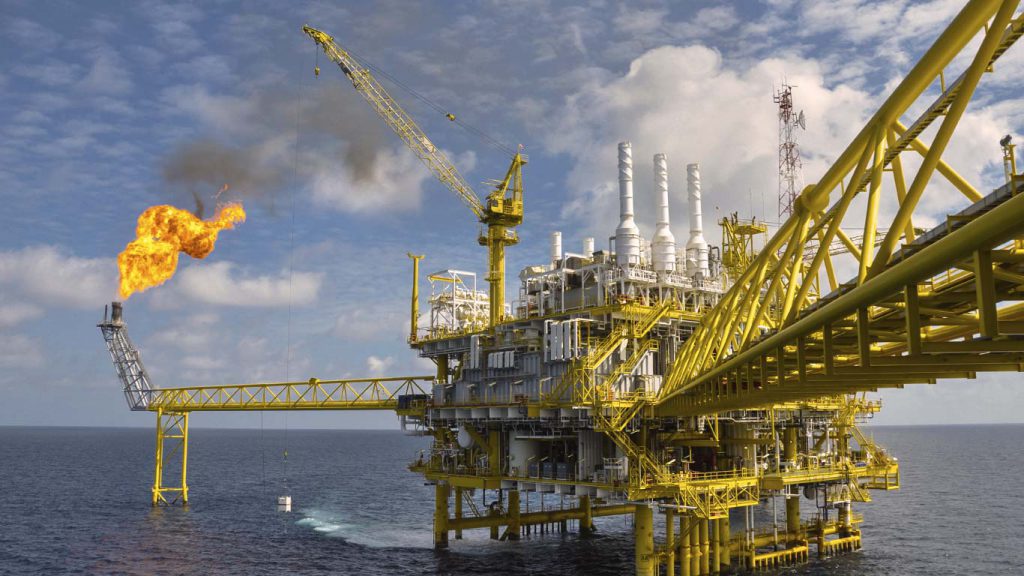
Gilsonite uses in Oil Sector
Gilsonite is used in drilling mud fluids and oil well cementing. Gilsonite, in a range of softening points and particle sizes, is a standard ingredient in oil-based drilling muds used in shales and other difficult geological formations. The addition of specially-treated Gilsonite to water-based drilling fluids helps minimize hole washout by stabilizing troublesome shales, and seals off highly permeable sands while reducing torque and drag. The addition of Gilsonite to oil well cements reduces slurry weight without loss of compressive strength and acts as an effective bridging and plugging agent to seal fractures in weak formations while cementing.
Gilsonite in drilling fluid loss control
For many years, Gilsonite has been used in the oilfield as an additive in drilling fluids. Gilsonite, in various grades and formulations, has been used to combat borehole instability problems, provide lubricity, especially in highly deviated holes, and more recently as a bridging agent to combat differential pressure sticking and provide a law invasion coring fluid. It has been well documented that appropriately formulated Gilsonite products can minimize hole collapse in formations containing water-sensitive, sloughing shales and reduce stuck pipe problems by forming a thin wall cake and an inter-matrix filter cake.
Gilsonite products are currently being widely used in water based, oil based, and synthetic based mud systems worldwide. Blended Gilsonite has proved to be very effective in all water-based systems.
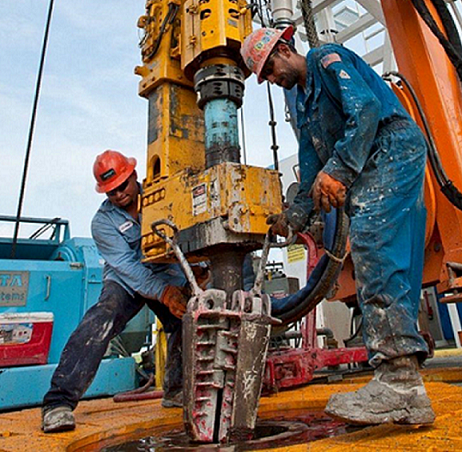
The role of drilling mud
Today, drilling fluid must meet at least ten requirements to be considered a good fluid.
- Cleaning of wells and transporting carcasses to the ground.
- Placing the wall and preventing it from slipping into the well and preventing the drilling mud filter from entering and causing damage to the tank.
- keeping the drill bit cool and clean during drilling.
- Oil drilling and drilling pipes.
- Control of underground pressures.
- Floating drilling rigs and fluid weight gain materials when pumps are off to prevent sedimentation, which can lead to drilling blockage and eventually residual or loss of wells.
- Hydraulic power transfer of pumps to drill by jet impact mechanism.
- tolarate part of weight of pipes according to its buoyancy properties.
- Reduce waste on adjacent formations.
The main functions of drilling fluids include providing hydrostatic pressure to prevent formation fluids from entering into the well bore .
There are basically three types of drilling muds:
1–Oil based Muds – OBM: Base material is Oil product, such as diesel oil
2– Water Based Muds – WBM: Base material is water
3– Synthetic_Based_Muds – SBM: Base materials is polymers
Gilsonite is vastly used in all drilling muds but in different aspects and manners.
In oil-based muds, Gilsonite acts as a Fluid loss control agent or FLC. While as a hydrocarbon, it reacts well with the base material of the mud and increases the drilling efficiency significantly. Also since Gilsonite has a high softening point, applying Gilsonite will significantly reduce the loss of fluids.
Gilsonite improves drilling efficiencies, wellbore stability,filter cake development and more.as an integral component of premium drilling fluid products ,Gilsonite actively improves drilling efficiencies while reducing costs and minimizing the HSE impact associated with most drilling fluid additives.An important characteristic of gilsonite is its softening-point temperature. In oil-base muds, it is used as a fluid-loss control agent. Being a hydrocarbon, it is naturally wetted by the oil. In water-base muds, it is used as a shale-stabilizing additive and is difficult to evaluate unless tested at or above its softening point.
fluid loss control:The act or means of controlling (usually lowering) the volume of filtrate that passes through a filter medium. Control of fluid loss for a mud is achieved by several means, one of which is by addition of fluid-loss-control materials for example gilsonite to the mud system.
Functions of Drilling Fluid loss control (FLC)
- Remove cuttings from the well.
- Control formation pressure.
- Suspend and release cuttings.
- Seal permeable formations.
- Maintain wellbore stability.
- Minimize reservoir damage.
- Cool, lubricate, and support the bit and drilling assembly.
- Transmit hydraulic energy to tools and bit.
- Ensure adequate formation evaluation.
- Control corrosion.
- Facilitate cementing and completion.
- Minimize impact on the environment.
- Prevent gas hydrate formation.
Gilsonite provides all of these benefits
- Provides wellbore strengthening matrix
- Controls fluid loss and seepage
- superior shale stabilization
- Prevents lost circulation
- Strengthens the wellbore to increase wellbore stability
- Minimizes differential sticking
- Reduces or eliminates lost circulation
- Promotes effective filter cake development
- Performs in oil- and water-based drilling muds
- Performs in HP/HT environments
- Minimizes HSE risks
HEALTH, SAFETY AND ENVIRONMENTAL ADVANTAGES
Gilsonite has significant health advantages over synthetic products like:
- Non-toxic (unlike coal or fly ash)
- Non-carcinogenic
- Non-mutagenic
Gilsonite Prevents Formation Damage
Gilsonite FLC Drilling Fluids prevents the shape of the well and the damage to the oil well
Due to the chemical and physical composition of the materials along the walls of the oil well, Gilsonite creates a very strong insulator without permeability against drilling fluids.Gilsonite FLC unique property in terms of its compatibility with the oil wells and the flexibility of Gilsonite prevents fluid leaks and changes in oil wells in reactive clay layers even in the hot temperature of lower elevation of the wells.
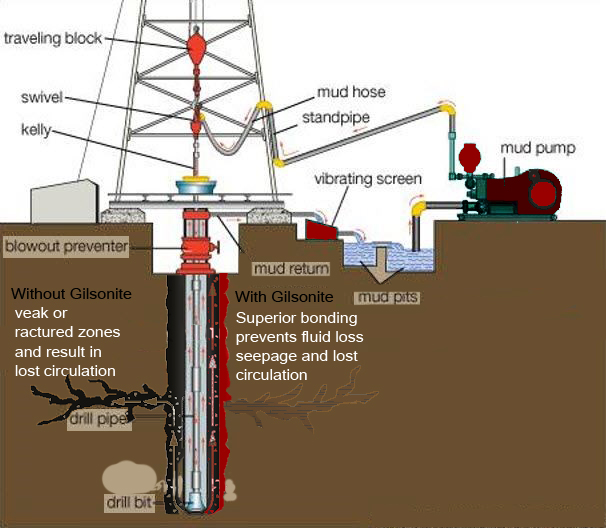
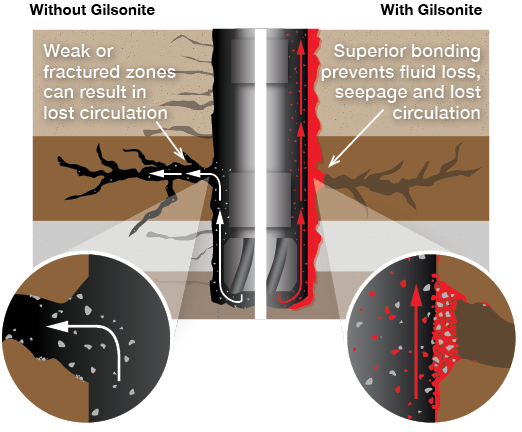
HP/HT wells, shales and underpressured zones require specialized drilling fluids and wellbore-strengthening techniques. Adding Gilsonite to an OBM, SBM or WBM strengthens the well by:
Reducing pore pressure transmission and sealing micro-fractures in shale and low-porosity sands,Keeping interbedding formations intact,Developing effective filter cake,Providing a “smear effect” that creates a continuous protective sealant along the wellbore wall.
COST ADVANTAGES of Gilsonite Compered to Alternative Products Like sulfonated asphalts
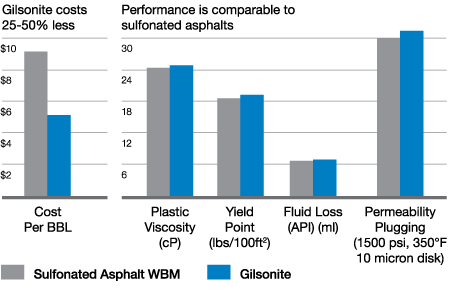
In stricter environmental drilling, where Synthetics Muds are used, applying Gilsonite may decrease the costs by 80% compared to the substitute material UHT-Co Polymers.
Packing of gilsonite in lump and powder form
For Drilling Fluid Loss Control
FLC in lump form like rock packed in 500~1000 kg jumbo bag.
FLC 200 mesh packed in 500~1000 kg jumbo bag.
Drilling fluid additive 300 mesh packed in 500~1000 kg jumbo bag.
Drilling fluid additive 30-40 mesh packed in 500~1000 kg jumbo bag.
Drilling fluid additive 100 mesh packed in 500~1000 kg jumbo bag.
Drilling fluid additive 300 mesh packed in 25 kg pp bag.
Drilling fluid additive 200 mesh packed 25 kg multi-paper bag.
Drilling fluid additive 200 mesh packed 50 lbs multi-paper bag.
Drilling fluid additive 30-40 mesh packed pp bag on pallet.
Analysis of drilling fluid loss control
NO | TEST | RESULT | TEST METHOD |
1 | ASH CONTENT,WT% | 5 | ASTM-D3174 |
2 | MOISTURE CONTENT,WT% | 1 | ASTM-D3173 |
3 | VOLATILE MATTER,WT% | 63 | ASTM-D3175 |
4 | SOLUBILITY IS CS2,WT | 81 | ASTM-D4 |
5 | SPECIFIC GRAVITY @25C | 1.11 | ASTM-3289 |
6 | NORMAL NEPTHAN INSOLUBLES,WT% | 79 | ASTM-3279 |
7 | COLOR IS MASS | BLACK | ———————- |
8 | COLOR IN STREAK OR POWDER | BLACK | ———————- |
9 | SOFTENING POINT,C | 210 | ASTM-D36 |
10 | PENETRATION @25C | 0 | ASTM-D5 |
ELEMENT ANALYSIS
1 | CARBON,WT% | 84 | ASTM-D5291 |
2 | HYDROGEN,WT% | 7.1 | ASTM-D5291 |
3 | NITROGEN,WT% | 3.67 | ASTM-D5291 |
4 | OXYGEN,WT% | 3.1 | ASTM-D5291 |
5 | SULPHURE,WT% | 4 | LEGO(S)ANALYSER |