General Defination of Bitumen Emusion
Bitumen emulsion is a liquefied type of bitumen with a low viscosity. By dispersing bitumen in water and adding an emulsifier, ordinary bitumen turns into a low viscosity liquid that can easily be used in a variety of applications, including repairing and maintaining roads, waterproofing, spraying, etc.. But as the bitumen is a petroleum product it doesn’t mix with water and as it is sticky in nature, it doesn’t easily get disintegrated into fine droplets. To overcome this problem an emulsifier is used.
Emulsions make it easy to handle, store, transport and apply bitumen at a lower temperature: Since this type of bitumen is liquid, there is no need to heat it before applying. Moreover, applying bitumen emulsions using cold techniques reduces the consumption of energy and makes road construction environmentally friendlier.
The emulsifier can be defined as a surface-active agent. Emulsifier keeps the bitumen in its fine droplet state by disallowing it to mix with other droplets. As the droplets are very fine they suspend in water. “Therefore, bitumen emulsion is a dispersed liquid consisting of three products, i.e. water, bitumen, and emulsion”.
Bitumen emulsion are usually two-phase systems consisting of two immiscible liquids, bitumen and water. The bitumen phase can be dispersed in the aqueous phase by mechanically shearing it in a colloid mill. The dispersion of bitumen particles is held in suspension in water by a chemical emulsifier which usually imparts an electrical charge so that the resulting electrostatic forces prevent the globules from readily coalescing. That is, like charges on each dispersed bitumen particle repel and prevent the particles from coalescing and settling from the suspension.
Emulsions can be used for almost any purpose for which conventional bitumens, polymer modified binders, and cutback bitumens are used, and are suited to a number of other applications where the use of cutbacks is not appropriate.
Therefore we can say that a bitumen emulsion is a liquid product consisting of three things, (i.e. water + Emulsion + Bitumen) where droplets of bitumen are suspended in water.
HOW IS IT PRODUCED OF BITUMEN EMULSION
The production of bitumen emulsion takes place in two simple steps:
Step 1:
Firstly, the water is mixed with the appropriate emulsifier and other chemical agents. The choice of emulsifier depends upon its ionic nature of the mix.
Step 2:
Now water emulsifier mix is added with bitumen in a colloidal mill. The amount of bituminous to be added depends upon the nature of the use of bitumen emulsion. If it is used for important works then between percent can range up to 60 to 70%.
The average range of bitumen mixed is from 40 to 70%.
The colloidal mill breaks down the bitumen into very tiny droplets. The average size of bitumen droplet is about 2 Micron. But the droplets try to join themself with each other and make it settle down.
But the emulsifier added creates a coating of surface charge around every drop droplet of the bitumen that helps to keep away from each other on the other hand it is also it also keeps the droplet in dispersed and suspended form. The mix received from the colloidal mill is stored in the storage tanks and used as per requirement.
Composition and Different Types of Bitumen Emulsion
The bitumen emulsion is classified into two types:
- Based on Setting Time
When the bitumen emulsion is applied on the aggregate for the road works the water evaporates leaving behind the bitumen droplets. These droplets spread on the aggregate and bind with each other and gains strength eventually.
Based upon the time taken by the vitamin emulsion to evaporate the water and between particles to separate from water, bitumen emulsion is further classified into 3 types based on setting time:
a) Slow setting emulsion
In this type of emulsion, a special type of emulsifier is used to slow the process of water evaporation. This type of emulsifier are relatively stable.
b) Medium setting emulsion
This type of bitumen emulsion doesn’t break as when applied on aggregate. The process of evaporation starts when the fine dust of mineral are mixed with the aggregate emulsion mix.
c) Rapid setting emulsion
This type of bitumen emulsion breaks down rapidly as it comes with contact with aggregate helping in fast setting and rapid curing.
- Based on Surface Charge
Bitumen emulsion is a combination of water and bitumen. As the mixture of water and oily products quickly separate, a third component is normally added to the mixture, in order to make it more stable.
Known as an emulsifier, this third component is used for making a mixture of water and oil dispersed in each other. In addition to their ability to reduce the tension between oil and water molecules, emulsifiers have an electronic charge that affects the molecules of bitumen emulsion and lead to the categorization of it into Cationic and Anionic.
- Anionic Bitumen Emulsion
- Cationic Bitumen Emulsion
In anionic bitumen emulsion, the tiny droplets of bitumen are electronegatively recharged. In Cationic bitumen emulsion, the tiny droplets of bitumen are electro positively charged.
The average and commonly used emulsions is cationic between emulsions.
Selection of positive or negative recharge between emulsions depends upon the mineral composition of aggregate on which it is used
Ex: In the case of silica-rich aggregates the surface of silica is aggregate is positively charged therefore cationic bitumen emulsion is used which helps in better spreading and binding of bitumen with aggregates.
The electronic charge of bitumen emulsion decides on what kind of surface it should be used. Some aggregates (such as marble aggregates) mix better with anionic bitumen emulsion and some others are a better solution to cationic bitumen emulsion (such as granite aggregates).
Both cationic and anionic bitumen emulsions are categorized according to the setting time. Look at the table below to find the various categories of bitumen emulsion and their globally standard names.
Classification of Emulsion Bitumen according to per setting characteristics
Bitumen emulsions are classified according to the sign of the charge on the droplets and according to their reactivity. Cationic emulsions have droplets which carry a positive charge. Anionic emulsions have negatively charged droplets. Rapid-setting (RS) emulsions set quickly in contact with clean aggregates of low-surface area, such as the chippings used in chip seals (surface dressings). Medium-setting (MS) emulsions set sufficiently less quickly that they can be mixed with aggregates of low surface area, such as those used in open-graded mixes. Slow- setting (SS) emulsions will mix with reactive aggregates of high surface area. RS emulsions are reactive and are used with unreactive aggregates; SS emulsions are unreactive and are used with reactive aggregates. The actual setting and curing time in the field will depend on the technique and materials being used as well as the environmental conditions. The complete list of emulsion grades is shown in the table below.
A suffix of “h” or “s” at the end of the emulsion grade indicates that a hard or soft base asphalt was used. Some anionic emulsions are designated “HF” for “high float,” which indicates that chemicals were used to give the asphalt a thicker film. When applied to an aggregate surface, this helps more of the asphalt film stay in place on the aggregate particles without draining into the pavement structure.
In the naming of emulsions according to ASTM D977 and D2397, cationic RS, cationic MS, and cationic SS emulsions are denoted by the codes CRS, CMS, and CSS, whereas anionic emulsions are called RS, MS, and SS, followed by numbers and text indicating the emulsion viscosity and residue properties. For example, SS-1H would be a slow-setting (i.e., low reactivity) anionic emulsion with low viscosity and a hard asphalt residue. CRS-2 would be a reactive cationic emulsion of high viscosity. The QS (quick-setting) and CQS (cationic quick- setting) designations for quick-setting emulsions have been introduced for emulsions intermediate in reactivity between MS and SS, which do not need to pass the cement mix test, and are used primarily in quick-set slurry surfacing applications.
Local authorities have many other naming schemes associated with emulsions with particular properties. In-state department of transportation (DOT) specifications letters such as P or LM may indicate polymer-modified or latex-modified asphalt emulsion, S may indicate high solvent content, and terms such as AEP (asphalt emulsion prime) and PEP (penetrating emulsion prime), and ERA (recycling agent emulsion) may indicate emulsions with specific uses.
Advantages and Limitation of Bitumen Emulsions
Advantage
- The strength properties of bitumen are preserved in emulsion mixes since emulsions do not need hot mixing. Generally, cold mixing or just slightly warming the ingredients of the emulsion mix are done for the construction of pavements.
- The emulsion can be used in wet weather even when it is raining.
- Emulsions possess anti-stripping properties.
- Emulsions with lower viscosity or thinner consistency improve spreadability and allow better coating of the bitumen on the surface of aggregate.
- There is no wastage during laying and storage.
- Since emulsions are water-based, there is less effect on the environment.
- It is the least energy-intensive of all construction material: there is no need to heat.
With viscosities in the range 0.5–10 Poise at 60°C, an asphalt emulsion is of considerably lower viscosity than asphalt itself (100–4,000 Poise), allowing it to be used at a lower temperature. Low- temperature techniques for construction and maintenance reduce emissions, reduce energy consumption, avoid oxidation of the asphalt, and are less hazardous than techniques using hot asphalt. They are also more economical and environmentally friendly than cold techniques using cut back asphalts. The environmental benefit of asphalt emulsion is particularly positive when used for in-place or on-site techniques which avoid the energy usage and emissions associated with heating, drying, and haulage of aggregate. The construction of a roadway with cold techniques has been calculated to consume approximately half the energy of one of similar bearing capacity made with hot-mix asphalt (HMA) An environmental impact analysis (EIA) technique called “eco-efficiency” has been applied to emulsion maintenance techniques (micro-surfacing and chip seal) and it was concluded that the emulsion system had less environmental impact than a thin hot-mix overlay.
Emulsions are water-based and in many cases can be diluted further with water for applications such as dust control and priming. They are also compatible with hydraulic binders like cement and lime as well as water-based polymer dispersions like natural and synthetic latex. When mixtures of cement, latex, and asphalt emulsion cure, a composite binder is produced with a structure that cannot be duplicated with hot asphalt and with significantly improved properties compared to pure asphalt.
Limitation
- No one type of emulsion is suitable for every work. it depends upon whether the aggregate is acidic or basic in nature.
- The setting time may vary depending on the air temperature, wind velocity, and type of emulsion.
- There is a wide range of curing time; a suitable emulsion mix needs to be designed for a particular need, i.e. we need to determine for each case, the optimum quantity of emulsion based on zone, type of emulsion, mix grade and desired mechanical properties
- It has limited storage time (ranging from a few days to six months)
FACTORS AFFECTING SETTING OF EMULSIONS
The following factors affect the setting & curing of bitumen emulsion mixes.
- Water absorption of aggregate
- The surface texture of the aggregate
- Amount of mineral dust in aggregate
- Aggregate gradation
- Mineral composition of aggregate
- The intensity of charge on aggregate surface
- Type of emulsifier used & its quantity
- Atmospheric condition, climatic conditions
- Wind velocity & altitude
- Drainage conditions at the construction site
Bitumen Emulsion Application
- Emulsions are used in bituminous road construction work. They are especially helpful for maintenance and patch repair works.
- The emulsion can be used in wet weather even when it is raining.
- Also, emulsions have been used in soil stabilization, particularly for stabilization of sands in desert areas.
- A rapid setting type emulsion is suitable for surface dressing and penetration macadam type of construction.
- Medium setting type is used for premixing with coarse aggregates.
- In the case of fine aggregates, the surface area of aggregate is more and as a result, a long duration of time is required to mix the emulsion. Therefore slow-setting emulsion is preferred which gives sufficient time for uniform blending of the mix.
The first asphalt (bitumen) emulsions used in road construction were prepared in the early part of the 20th century. Today approximately 3 million tons of emulsions are produced in the United States representing about 5% to 10% of asphalt consumption. More than 8 million tons of emulsions are produced worldwide. Emulsion production varies greatly among countries with the United States, France, Mexico, and Brazil being significant producers
What Factors are Important in Grading Bitumen Emulsion?
Viscosity
The first vital factor for grading bitumen emulsion is the viscosity value. The viscosity of bitumen emulsion is determined by its bitumen content. An emulsion with small droplet size and a narrow distribution will give a higher viscosity.
Ductility
To indicate the bitumen resistance to breaking, a ductility test is done. This testing system measures the extent to which a sample of bitumen can stretch before breaking. A bitumen emulsion that its ductility is more than 40 cm makes the surface of a road safe and strong to heavy traffic and do not break easily.
Penetration
The softness level of bitumen is indicated by entering a standard needle into it. The harder the bitumen, the better it is for using in hot temperatures. The standard range of penetration can vary among different grades of bitumen emulsion
Techniques & Usage of Bitumen Emulsion
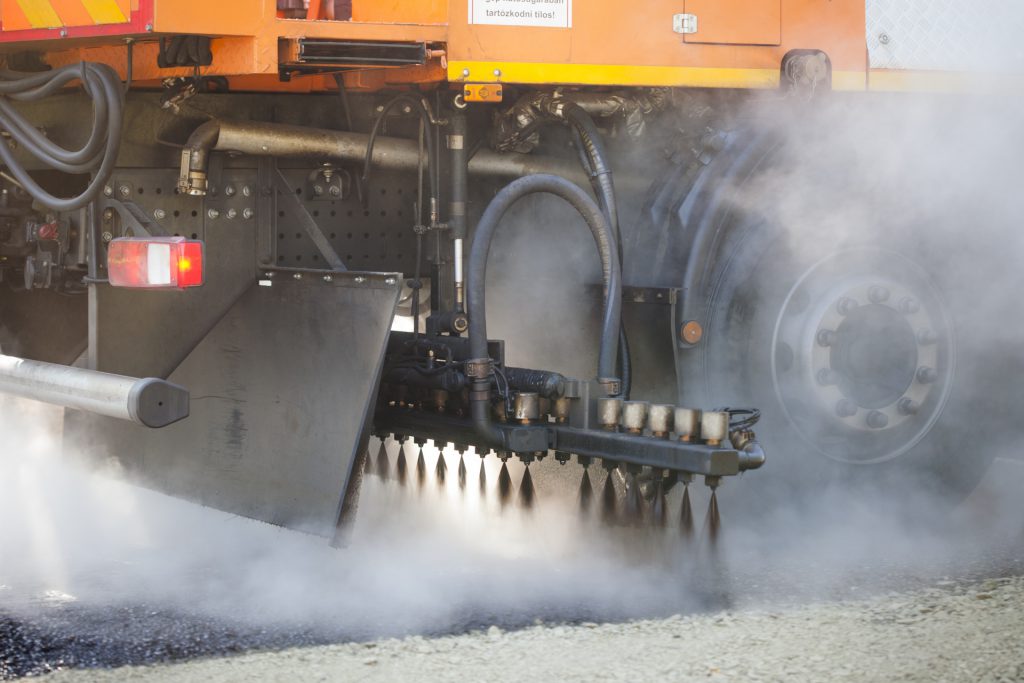
Emulsion Asphalt
Routine repairs, structural maintenance, wearing course maintenance… Bitumen emulsion techniques can meet your needs to maintain the long term serviceability of your pavement. Emulsion techniques are energy-efficient and limit greenhouse gas emissions.
Cold asphalt mixes for surface courses
Cold asphalt mixes are made with high-quality aggregates and are often used in surface courses as the final road pavement.
The design of cold mixed asphalt concretes usually utilize 0/10mm or 0/14mm aggregate and a selected bitumen emulsion. These types of cold mixes offer the following advantages:
- Low impact on the environment.
- Ease of use (as they are stable and remain workable for several hours).
- Remain flexible over time and are compatible with a wide range of underlying pavement materials.
The performance of bitumen emulsions makes it possible to obtain cold asphalt mixes with a good macrotexture, and adhesion characteristics equivalent to those of hot asphalt mix materials.
Due to their qualities, cold asphalt mixes are particularly well suited for:
- Pavements located in difficult climate zones (e.g. mountains, etc.).
- Pavements that are not heavily structured.
- Pavements subjected to low to average traffic (T2 or 300 heavy goods vehicles per day and per lane).
They are best applied with a paving machine/paver, with an average material course thickness between 30 and 50 mm.
Micro-surfacing using bitumen emulsion for surface courses
This technique constitutes the thinnest mixture that can be used as a surface course. Micro surfacing is the intermediary between a surface dressing and very thin asphalt concrete.
Micro surfacing protects the underlying pavement by improving impermeability, provides excellent adhesion to the existing road, compensates for small deformations, and has no loose aggregates under traffic.
The use of modified bitumen emulsion provides a good level of adhesion and flexibility over time. The relative simplicity and the speed of laying Micro surfacing minimizes the work time.
The latest technical enhancements with these products guarantees rapid reopening to traffic and significantly reduce the inconvenience for road users.
Micro-surfacing is well suited to the maintenance of rural roads, urban roads, highways and airfield runways. In some countries, it often constitutes the wearing course on”grave-emulsion”base course surfacing.
Surface Dressing for the renovation of wearing courses
Most importantly, road surfaces must remain impermeable and ensure good adhesion to the existing pavement. Based on these parameters, this surface treatment has always satisfied clients due to its relatively low cost.
The daily outputs are also quite high as the Surface Dressing is rapidly applied. A surface dressing restores skid resistance and seals the road to prevent water ingress.
Surface dressings with bitumen emulsion offer some significant advantages that include: they are not very sensitive to water and to weather conditions, they allow for the spreading of the work over the course of a relatively long season and they overcome the potential problem of moist aggregates.
A variety of surface dressing treatments are available to address the specific problems of each pavement to be treated.
For high traffic or difficult conditions, the modification of the bitumen emulsions by the addition of polymers brings clear improvement to the performances of the surface dressing.
The use of these modified emulsions has become the norm in many countries. A surface dressing with bitumen emulsion is a rapid and economical solution for the renovation of the existing pavements. Its qualities also make it very environmentally-friendly.
“Grave-Emulsion” for pavement resurfacing and reinforcement
Grave-Emulsion is an asphalt mix obtained from a mixture of aggregate, water and bitumen emulsion which is dosed and mixed cold. This type of treatment offers the following advantages:
- Low impact on the environment
- Ease of use
- An ability to regulate existing pavements and major deformations.
Grave-Emulsion is an ideal product for the resurfacing and reinforcement of low trafficked roads as well as those that are experiencing an increase in traffic.
Grave-Emulsion has been used for more than 40 years on pavements receiving up to 300 trucks per day and per lane. The typical application thickness is around 50mm.
If the aggregates used to allow for it, Grave-Emulsion surfaces can be driven on for several months, possibly even several years, before receiving the final wearing course as a step in the progressive development of the road. The final surfacing course is a surface dressing, micro surfacing or a cold asphalt mix.
Recycling of pavements on site using bitumen emulsion
Recycling with emulsion allows for the reconstitution of an improved quality road structure by reusing the existing road materials.
The work is mostly carried out in-situ using specific milling / mixing equipment, this shortens the overall project completion, and limits inconvenience for road users by allowing more rapid reopening of the road to traffic.
On-site recycling follows the principles of sustainable development as:
- Cold recycling saves energy,
- Eliminates the majority of transportation costs as the process minimizes the use of outside materials,
- Minimizes worksite waste
This process also offers the following technical advantages:
- It improves the overall homogeneous road structure,
- It improves rideability of the road
- It treats interface bonding problems,
- It improves impermeability of the road structure
- It conserves the finished pavement levels to minimize further costs
This technique, which has been used in Western Europe and the USA as well as many other countries worldwide for the past 30 years, is now an accepted tool for the road maintenance engineer. Recycling can be carried out on-site or in an offsite plant
Routine repairs of low-traffic roads: surface treatments and emulsion asphalt mixes offer the best solutions
As part of its responsibilities, a road management authority must frequently deal with urgent needs for repairs of sudden and localized degradation problems of the highway network: potholes, deformation of the support, cracking, trenches, etc. These repairs are considered urgent because of the need to protect the safety of users and to preserve the road.
When the degradation does not affect the impermeability of the pavement, the appropriate solution is the application of an emulsion surface treatment. The modest scope of the areas to be treated allows for the use of automatic patching equipment or even manual application. Automatic patching equipment guarantees perfect control of the dosing and the quality of the application.
Where degradations affect the surface course throughout its thickness (e.g. potholes and deformation) the solution to these flaws requires the use of asphalt mixes. Emulsion asphalt mixes are often an excellent solution as they can be stored, they are easy to use, and they are relatively insensitive to climatic conditions. Depending on the thickness of the repair, the cold asphalt mixes can be in the form of 0/6mm to 0/14mm emulsion stabilized aggregates or 0/6mm or 0/10mm cold asphalt mix.
The fact that it can be stored (from several days to several months) makes it suitable for emergency work. Its packaging in buckets also allows for long-term storage. For the topping up or filling of trenches, these emulsion stabilized aggregates or cold asphalt mixes can make up a base course and/or a surface course for temporary and permanent solutions.